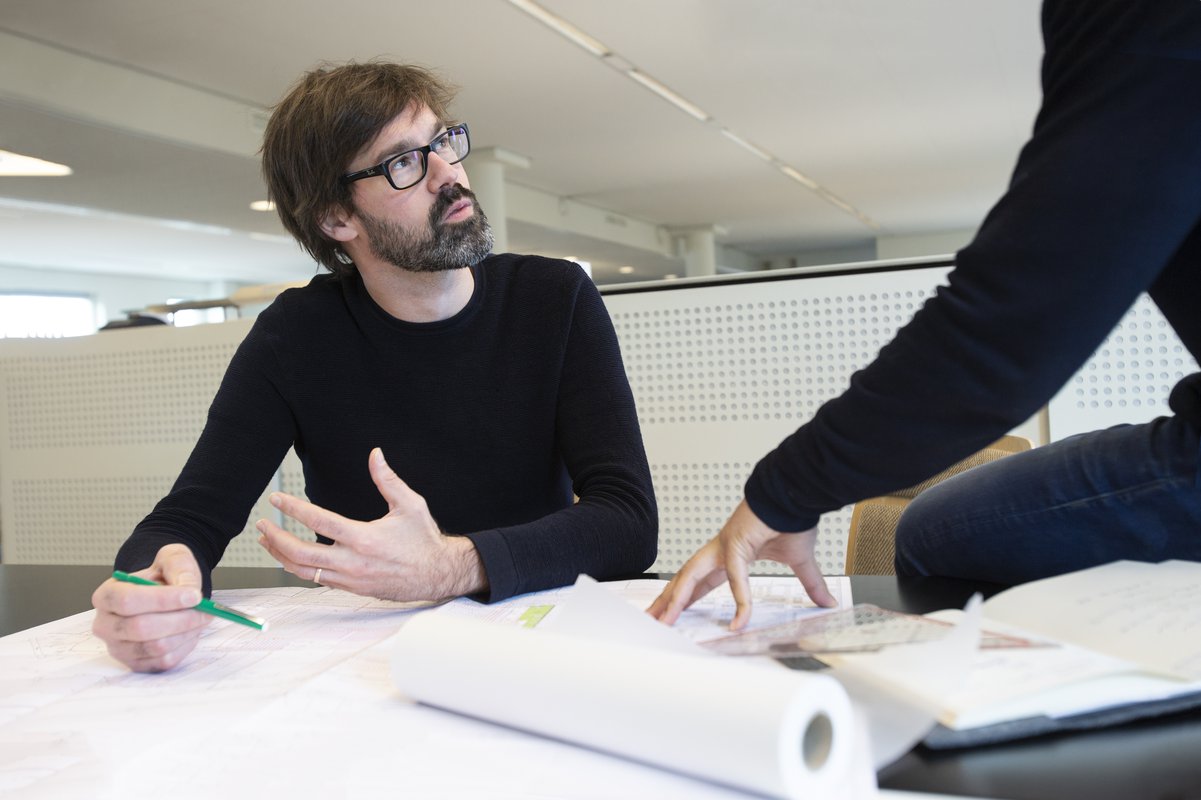
Nationale-Nederlanden asked you to make a circular design. How was that for you?
Twan: We were very excited that for this project, it was the client coming to us with great ambition regarding sustainability instead of us having to tell them. We have been putting effort into making our projects sustainable for some time, and now we have a client embracing the principles of 100% circular and Zero Waste!
How and when did you start the project?
Dirk: We really got going on the project back in 2019. It was a phased project as some of the employees would continue to work in the buildings during construction. The COVID-19 crisis also shook things up, stirring the project in terms of functions and square metres. For example, having people work from home more structurally as well as changes to the types of work activities conducted at the office.
We started the design process by holding several workshops with the client. We collaborated with stakeholders and working groups to collectively figure out how we could implement new ways of working for Nationale-Nederlanden. Additionally, we used information from a survey among all employees, which provided even more insight regarding the types of activities conducted and the desired associated facilities. It led to a detailed analysis of what is needed now and in the future.
When we start a design process, we initially think about rooms, not materials. We soon found out that for Haagse Poort, we wanted to focus on improving the sightlines. For this effect, we suggested transparent fire separations and harvested the glass building blocks – popular in the seventies – to create furniture.
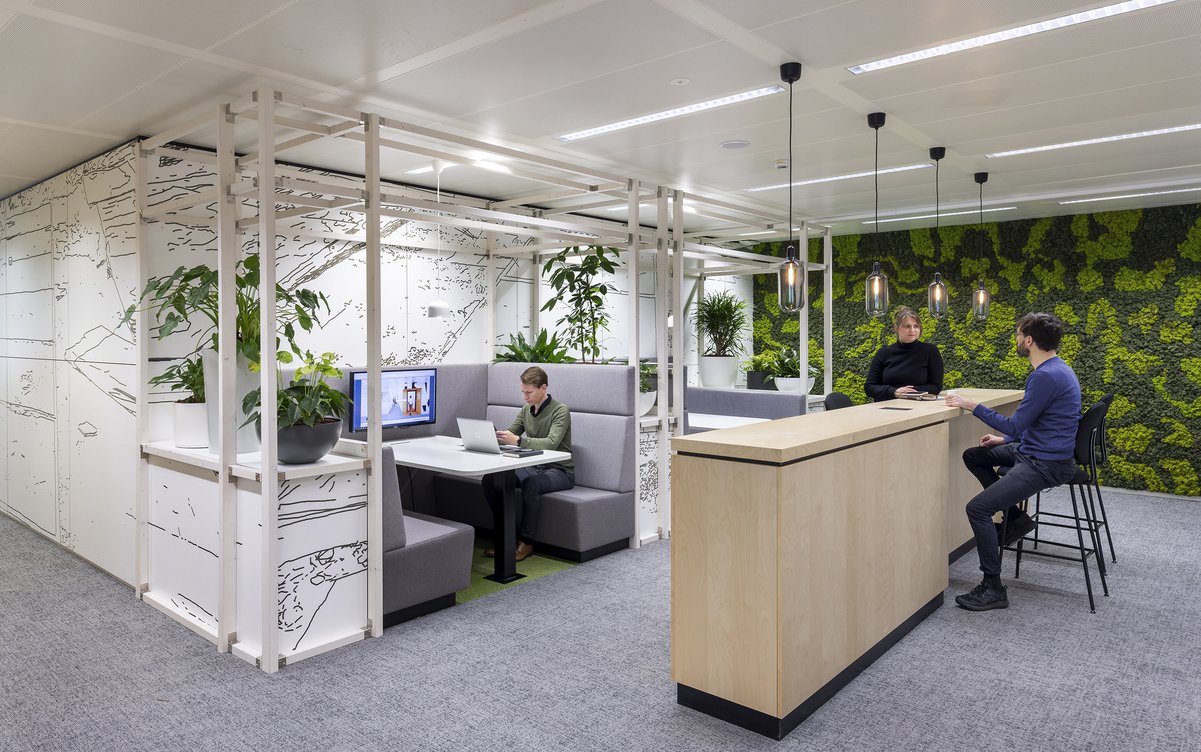
How did you go about reusing the old furnishing?
Twan: The ambition was to have no waste, so we looked at all elements of the existing furniture to see what could have a second life at Nationale-Nederlanden, or if we had to find a new use for it, ranging from upcycling to dismounting or, in the worst scenario, pulverising for tarmac in road construction. That was the worst option.
Dirk: We were able to reinstall all the custom-made objects in both buildings. For example, office train booths found a new place in the design, with new sustainable fabrics. The old materials were reused for acoustic panels. We could also give all pantry furniture a second life, mainly because it still looked new! The only thing was that the backs were not finished as they previously stood against the wall; so, they needed new covers.
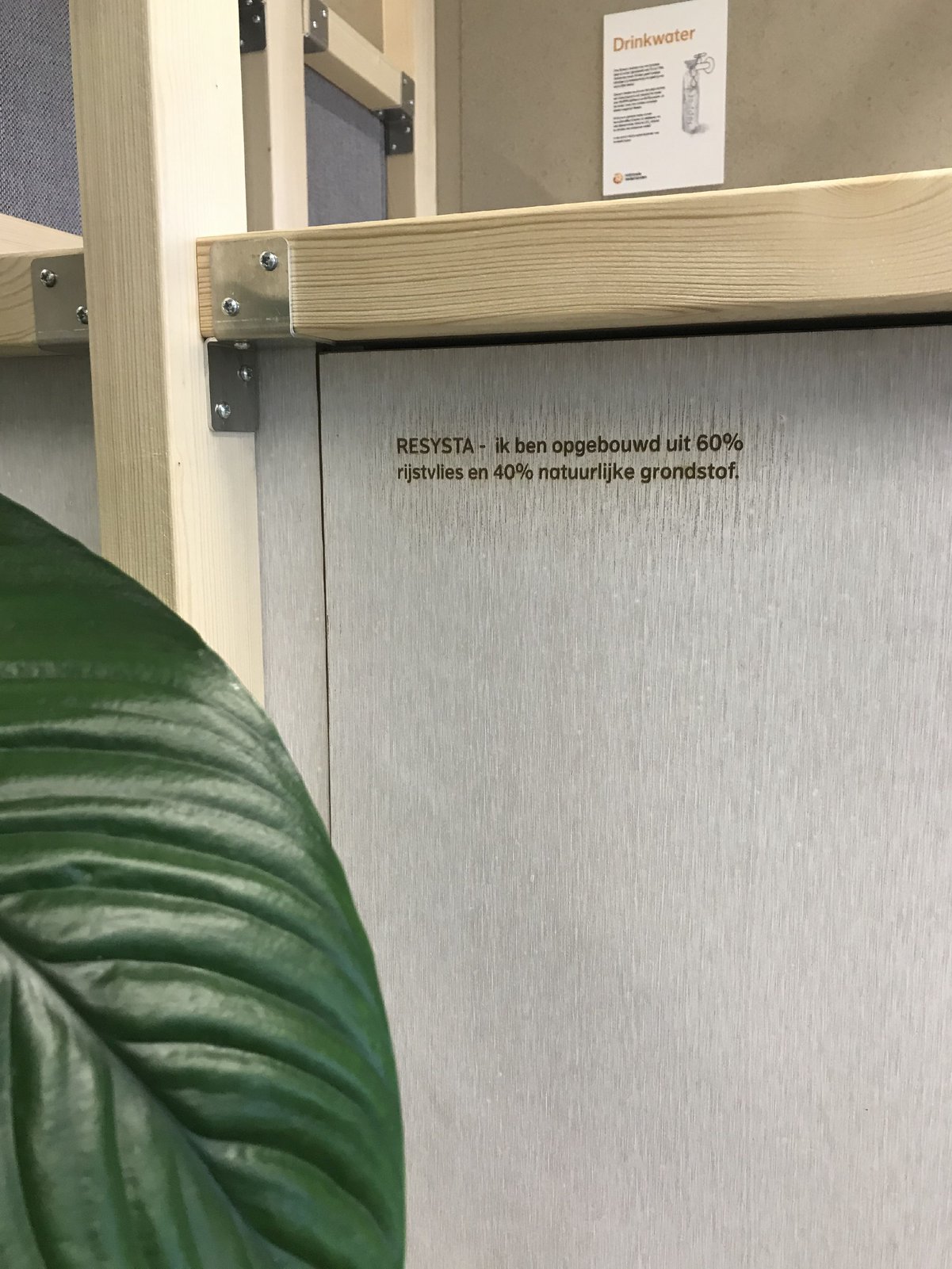
Twan: I thought it surprising how we reuse carpeting. Over time, many different types of carpet tiles were laid, of varying quality. At first, I thought we would be re-using the newest carpets, but we ended up taking the oldest ones as they are fabricated in a way that the different materials cannot be separated anymore, making them impossible to recycle. However, they were easy to clean and very durable. The newer carpets have an eco-backing which makes them better suitable to disassemble, so they were taken back by the manufacturer.
Dirk: Stuck with the old and coloured carpettiles we had to change plans because this wasn’t precisely the palette we had in mind. But the only alternative was that it would be thermally processed into tarmac...
Then we looked each other in the eyes and said “OK, we’re going to re-use it.” After all, we managed to create a nice plan with bright green and orange. Finding the right direction in Haagse Poort can be challenging because of its structure of long passages that make you lose your orientation. Colour can then be a suitable means of communication. In addition, we used moveable furniture to create a serene basis.
How did you keep track of all available materials and elements?
Dirk: All parties collaborating on this project had to record their activities in a digital environment called Project Place. It was a humongous Excel sheet managed by LBP|SIGHT. It worked as a joint live mining chart that everyone could always consult to see what was available and where it would be deployed. It drove us crazy, as it was so much work to keep it up to date. Everything had to be marked: Is it new, where does it come from, and so on. It was a real challenge to all involved. Every day, something could change, disappear, or appear anew.
Twan: At some point, the contractor started dismantling walls, and behind a panelled wall, another older plasterboard wall was concealed. Since we wanted zero waste, we had to find a solution for that too. It kept us busy finding solutions.
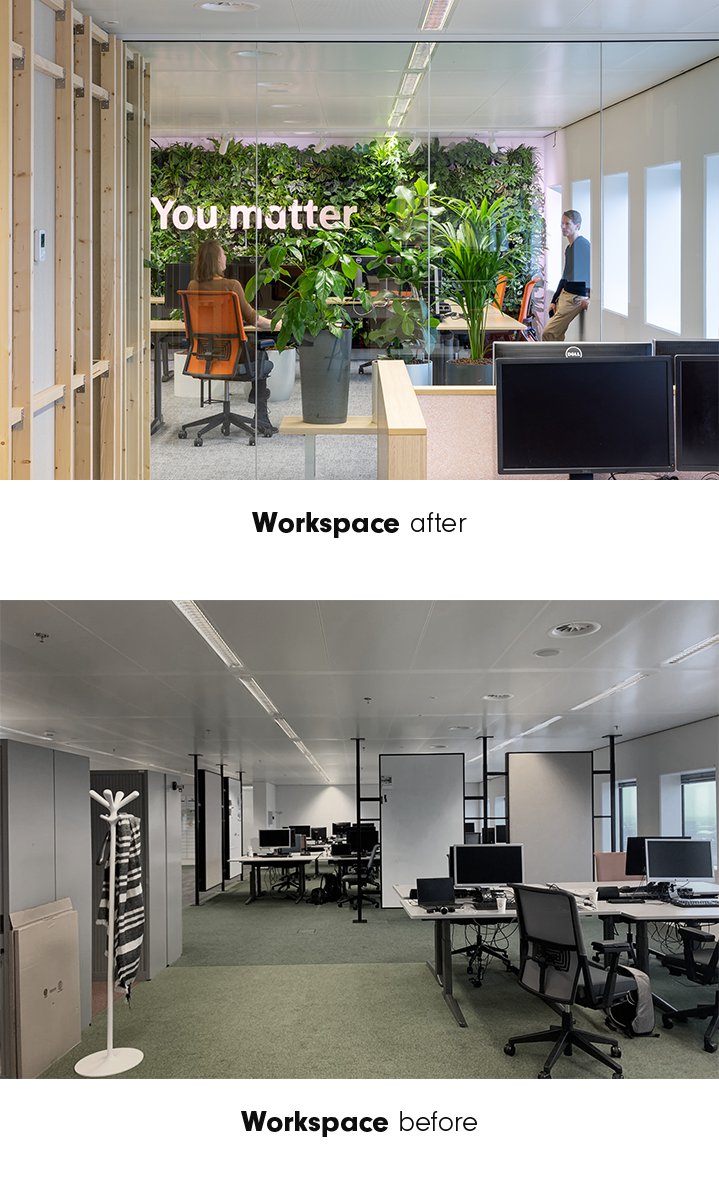
You worked on two buildings simultaneously. Did you mix the materials?
Dirk: Yes. That was no problem for the custom-made objects but more difficult for the modular partitioning because of the differences in height.
Twan: We thought of a few tricks. We had harvested modular partitioning in Ede with a height of two metres forty. You can always top it with a cove. The underlying idea was to use all the materials as efficiently as possible. When the interior builder had spare panels, the wall builder could use them and vice versa.
Were you able to construct everything with repurposed materials, or did you also introduce new materials?
Twan: We used materials that did not originate directly from Nationale-Nederlanden, such as the one hundred square metres of white Trespa panels used to create a large artwork that runs through all floors. We found the panels on Superuse’s urban mining chart in several old buildings in Rotterdam.
Our last option was to resort to some new materials as well. In that case, we looked for materials that had been produced as sustainably as possible, for instance, locally, cradle-to-cradle, or bio-based.
Did you make any discoveries with that?
Dirk: yes, in particular, for the post-COVID wings, in which we focused on hybrid working, we searched for innovative materials. Then you notice that many things are still in their infancy. If you try to achieve an ECI as low as possible, some inspiring new products cannot be used yet because they are still being developed, and their rating is still low. That is a pity because we wanted to give start-ups with interesting new products a chance. You have to be aware of greenwashing; If you ask a few more questions or have the environmental costs calculated, many products score well in one area but not overall. It made us all pioneers in that regard. The focus of a circular construction project is on collaboration in particular.
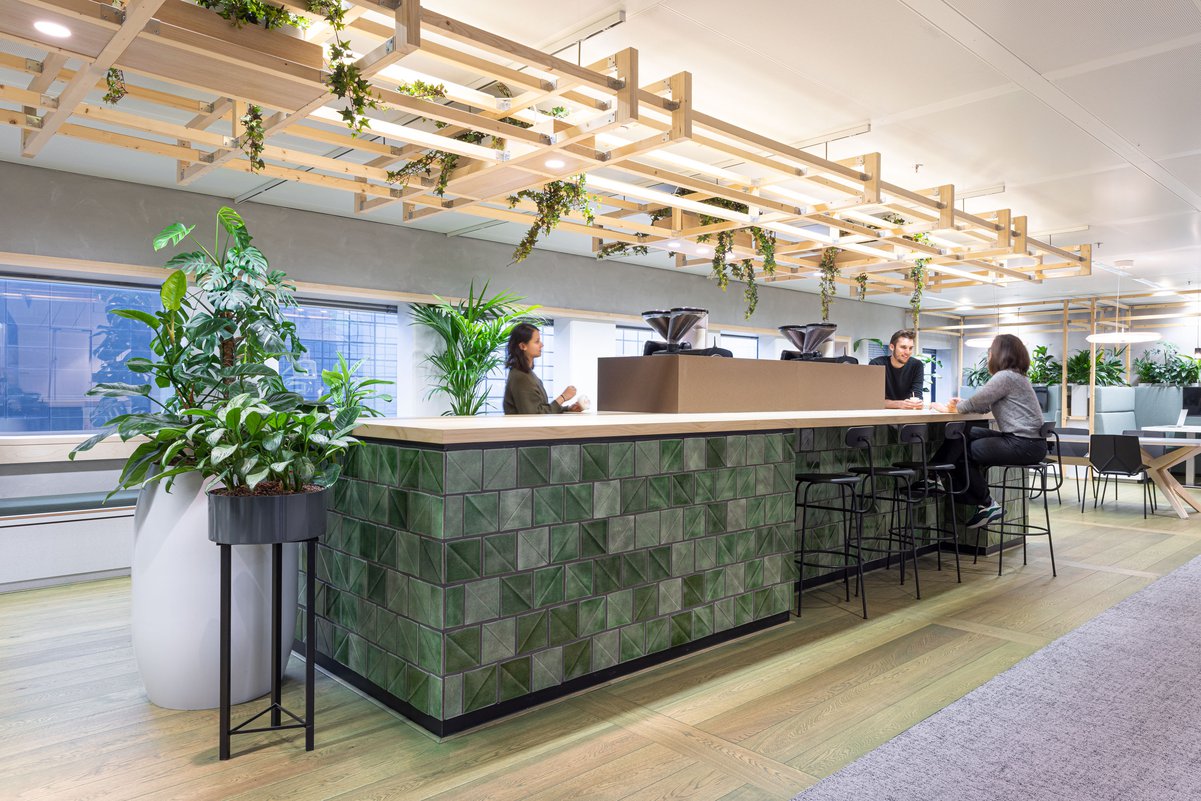
How did that affect your process?
Dirk: In the initial phase of the design, we started with the spatial layout while also offering early suggestions on the types of materials we were thinking of, in terms of specifying a wooden floor in this area, greener over there. Compared to others, a distinctive difference with this project is that we would normally take this initial design and detail it into a final one. Here we kept to making visuals which instead explained what we were conceptually looking for. We produced a kind of design manual which we used to challenge the contracted parties to come up with materials which would fit the circular design and Zero Waste ambitions. Subsequently, we worked in joint collaborative sessions on the final execution of construction details. It allowed us to reuse the existing materials in the new environment properly.
For example, we made a design for a pantry with green tiles, and Gielissen came up with a product made from building debris they found in Germany. In another pantry, we defined a kind of metallic panel, and then they proposed to use an HPL panel made from coffee grounds, which sounded very nice and to the point.
The interior builder also looked at how the panels had to be sawn so that there were as few leftovers as possible, and even the sawdust was collected to press new plates. Sometimes the visual result would be different from what we had in mind originally. The volume remained the same, but the size of the wood would be different.
When you use a manual instead of a set of drawings, who makes the final decisions about the design?
Dirk: We will make the drawings together, which is why this phase will consume much more time. We maintain the supervisor role; explain the design principles, and the constructing partners will advise from their expertise.
Does this change the role of the architect?
Dirk: There are many types of designers, including those who want to be left alone entirely so they can devise everything themselves. In a circular process, you have to be more flexible, but personally, I like having to work with all pieces of the puzzle. Besides that, we really have been designing. An example is the mounting plates we used for the wooden frames. They were perforated from recycled aluminium panels. When we saw those plates at Gielissen, we had the idea to use the remainders for the movable panels in the meeting rooms. By leaving some of the perforations of the boards out, we achieved a more playful effect.
Twan: To me, the architect’s role changes into more of a team player. At the same time, I noticed that a process might go on endlessly if everyone keeps considering the alternatives. It’s essential to keep your position as the owner of the aesthetic design if you want to advise the client properly.
Read the full publication at this link: PDF publication in Dutch
A publication by Nationale Nederlanden;
Written by Marieke van den Heuvel, MANN office;
Photography Lucas van der Wee.